- Safe travel escort | Jincai New materials to carry out a full range of vehicle maintenance knowledge and skills training!
- The characteristics of polypropylene masterbatch are mainly reflected in the following aspects.
- The operation of the textile industry from January to October 2024!
- National fire · life first | Golden Color New Materials Union participated in the 10th Yuan Hua Town staff fire emergency skills Competition!
- What are the advantages of polypropylene masterbatches?
- Textile industry leads new quality productivity!
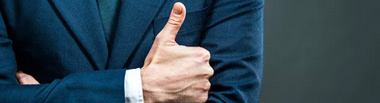
- Contact: Ms. Yang
- Phone: 0086-159 8831 5556
- Tel: 0086-573-87656555
- Fax: 0086-573-87659333
With the rapid development of China's economy, masterbatch industry is also accompanied by the development of related industries and the substantial development of masterbatch production technology has also been an unprecedented level of improvement, masterbatch applications are constantly expanding. However, due to the impact of traditional Chinese market competition, often the pursuit of "low-quality, low-cost, can be used", resulting in downstream masterbatch production is not stable enough, low-grade quality, product competitiveness is not strong, the problem has been Many masterbatch manufacturers have been widely recognized, especially the high quality requirements of polypropylene manufacturers pay more attention to the quality of masterbatch on the quality of polypropylene. To this end, according to the requirements of polypropylene fiber chemical industry associations, to discuss the impact of masterbatch on the quality of polypropylene
First, the masterbatch in the dispersion of polypropylene fiber
With a variety of colors of polypropylene fibers, pigment particles are dispersed in the polypropylene fiber due to the key is the pigment particles are fully refined and in the polypropylene fiber evenly distributed (mixed). The fine dispersion is that the pigment particles are sufficiently finely divided and uniformly distributed (mixed) in the polypropylene fiber. Fine dispersion is the pigment aggregates or aggregates broken, so that the particles to a minimum, and the key lies in uniform dispersion, the effect of dispersion on the color of polypropylene fiber color, transparency, gloss, fiber strength, elongation, aging resistance , Power frequency and so have an impact.
In general, the pigment dispersed particle size is less than 1um can be used for fiber or ultra-thin film, and greater than 5 um will lead to fiber surface matte, greater than 10um will result in fiber surface spots, streaks, and with particle size The breaking strength and the elongation of the big fiber decrease continuously. The finer the particle size, the stronger the dispersion, the smaller the particle size, and the larger the hiding power.
Because the pigment particles state of primary particles, aggregates, aggregates three, and general merchandise pigment particles are larger than the aggregate particles (about 75-250um), it must be dispersed treatment, the so-called pigment dispersion will be reunion Body smashing process.
Pigment dispersion, the first wetting agent with a wetting pigment, coated on the surface of the pigment, so that the cohesion between the pigment to reduce the crushing pigment aggregates the energy required, followed by the crushing of pigment refinement, leading between the pigment particles Of the free movement (impact stress)
And the pigment aggregates break the aggregate particles by the shear stress of the surrounding medium.When the pigment is finely dispersed, the particle size decreases, the surface area increases, and the free surface energy of the pigment increases, resulting in fine pigment instability , So the surface of the coating to be further coating to reduce the surface of the newly formed surface energy, to prevent re-cohesion, and then the pigment mixed in the melt dispersion, the wetting and crushing of the pigment evenly distributed to the need to color the material Lt; / RTI & gt;
Second, the masterbatch performance and quality requirements
1. Performance requirements of polypropylene masterbatch
Polypropylene is a pure hydrocarbon, the molecular chain contains tertiary carbon atoms, heat, light by the tertiary carbon atoms in the molecule easy to crack, so that the quality of polypropylene deterioration, it is required to make the masterbatch in high temperature spinning Easy to spread, do not damage the fiber quality, do not make the fiber fade, excellent light resistance, wear resistance, solvent resistance, can withstand rigorous spinning draft.
(1) heat-resistant masterbatch selected pigments, the most basic requirements can withstand the temperature of polypropylene fiber production process, to maintain its performance and stability. Temperature requirements of the general requirements of 270 ~ 280 ℃ or more.
(2) Dispersed masterbatch pigment should be excellent dispersion, but also in the masterbatch to be dispersed, and the use of dispersing agent will not reduce the quality of polypropylene fiber. Otherwise it can not produce good quality liquid coloring fibers, running is not stable, when the fiber is easy to break or produce abnormal fibers.
(3) Brightness Polypropylene liquid coloring has a variety of uses, which for bedspreads base fabric and knitted fabrics, require bright colors. Because the organic pigments are bright and bright, and easy to color, so where used in the use of the need to use organic pigments.
(4) light resistance in the role of light under the action of some pigments have photosensitivity, so that colored fibers fade and brittle damage, and the pigment light resistance is basically related to its chemical structure, so in the production of masterbatch should pay full attention to pigment light resistance , And when it is necessary to use a light fastness pigment, it is conceivable to add an ultraviolet absorber.
(5) stability of masterbatch used in pigments, the color of polypropylene fiber to have excellent stability. This means that the pigmented polymer will not react with the fiber when exposed to heat, light, or heat at high temperatures for a long period of time, resulting in a new chemical group that renders the polymer low in performance. So the masterbatch should be used as pure pigment, without iron, copper, lead and other impurities in the salt to ensure that the physical properties of colored polypropylene fiber is excellent.
(6) water resistance, dry cleaning resistance, oil resistance, coloring polypropylene fiber products in use and inevitably go through washing or solvent dry cleaning, to contact with the oil, especially for the carpet, so its use of colorants to Have good washing resistance, dry cleaning resistance, oil resistance.
2. Quality requirements of polypropylene masterbatch
Masterbatch quality indicators include more content. Such as the appearance of the general size of 2 mm × (3 ~ 4) ㎜, masterbatch in Yan
Melting point, DF value, MI value, heat and weather resistance characteristics of the material particle size ≤ 1 um is more than 90%. These indicators are the masterbatch plant, polypropylene fiber plant issues of common concern.
(1) Filtration performance Fiber grade masterbatch with filter performance to characterize the quality of masterbatch, its value is called the DF value is small, the spinning process of the filter component replacement cycle is relatively long, generally require polypropylene masterbatch DF value Less than 2.0 x 105 Pa · cm 2 / g.
(2) melting point of polypropylene masterbatch dispersant using low molecular weight polyethylene wax, so the melting point of 110 ~ 120 ℃; and the general melting point of the pigment is high, more than the temperature of polypropylene spinning, so masterbatch in the thermal analysis There are two endothermic peak.However, the high and low melting point of masterbatch can not characterize the quality of masterbatch masterbatch, and some enterprise standards in the provisions of the melting point of 130 ~ 160 ℃.
(3) Melt flow index (MI) The MI of the polypropylene section is mainly used to characterize the molecular weight of the chips and determine the processing and finished product properties of the chips after they are cut into pieces. The masterbatch contains pigment, dispersant and carrier low molecule Polyethylene wax, it can not be used to express the level of MI molecular weight, and will be due to different pigments and varieties change, so masterbatch MI is not the masterbatch control index, only for spinning reference. Select the spinning masterbatch MI than the color slice slightly larger, beneficial to both the size of similar and mixed. General requirements for the MI value (15 ~ 30) g / 30min. (4) heat resistance Masterbatch heat resistance index refers to the masterbatch and polypropylene slices according to a certain percentage, respectively, at different temperatures to 5 to 10 minutes cycle spinning to observe the degree of color change. Color change can be used to assess the color change with a gray-like color card or color card comparison assessment, when its total color difference ⊿ E ≤ 3, the temperature is the masterbatch heat-resistant temperature, generally require heat 270 ~ 300 ℃, color change for the four.
(5) Weatherability coloring Polypropylene weathering, with reference to textile light fastness test method, the results with the assessment of the standard blue color fastness to assess the requirements in the light fastness 5, the fact that more than in the 6 ~ 8.
Third, the use of masterbatch points
(1) choose masterbatch, according to the selection of selection, polypropylene masterbatch fine denier, coarse denier-level, coarse denier-class masterbatch color can not be used for fine denier color, color should be considered Spinning fiber single denier, select the same level of masterbatch.
(2) the choice of the masterbatch is the best manufacturer of the same products, in order to reduce costs should be selected high-concentration masterbatch. Color Masterbatch of high, medium and low-grade points, color should be based on fiber quality requirements, the appropriate choice of different levels of masterbatch. To avoid the pigment light, thermal stability caused by the different quality of finished fiber variation, color matching should also be selected in line with fiber quality requirements, with the same light and heat stability level of color masterbatch, crude fiber than the concentration of fine fibers Low, the masterbatch proportion is proportional to the square root of the denier.
(3) in order to reduce the color after the color fiber, the masterbatch to be diluted to control the mixing ratio of filaments of not less than 3% to 10%, staple fiber of not less than 1% to 3%, monochrome continuous The yarn is spun with a trichromatic device and the masterbatch must be fed to the extruder after mixing
- Safe travel escort | Jincai New materials to carry out a full range of vehicle maintenance
- The characteristics of polypropylene masterbatch are mainly reflected in the following asp
- The operation of the textile industry from January to October 2024!
- National fire · life first | Golden Color New Materials Union participated in the 10th Yua
- What are the advantages of polypropylene masterbatches?
- Textile industry leads new quality productivity!
- Transformation and upgrading of textile and garment industry!
- Golden Color New Materials congratulates 2024 National plastic coloring and color masterba
- Plastic exhibition ended successfully | Golden Color won the honorary title of
- The operation of the textile industry from January to August 2024!