- Safe travel escort | Jincai New materials to carry out a full range of vehicle maintenance knowledge and skills training!
- The characteristics of polypropylene masterbatch are mainly reflected in the following aspects.
- The operation of the textile industry from January to October 2024!
- National fire · life first | Golden Color New Materials Union participated in the 10th Yuan Hua Town staff fire emergency skills Competition!
- What are the advantages of polypropylene masterbatches?
- Textile industry leads new quality productivity!
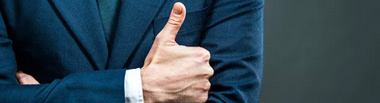
- Contact: Ms. Yang
- Phone: 0086-159 8831 5556
- Tel: 0086-573-87656555
- Fax: 0086-573-87659333
The advantages of polyester masterbatch
Release date: [2017/8/4]
Read total [369] times
The advantages of polyester masterbatch
(1) easy to use
Spinning before the color of polyester production, fiber use without any special requirements, the original spinning equipment, the existing production process. Especially when the polyester and other fibers blended intertwined, the use of polyester fiber does not only reduce the dyeing process, so that is not suitable for high temperature, high pressure dyeing conditions of fiber and polyester blended intertwined and easy to achieve the fabric pre-designed style. So before the spinning color to a certain extent, it can be said that no investment in the dyeing plant, is to use advanced technology to solve the dyeing and finishing "bottleneck" one of the shortcuts.
(2) low cost:
The cost of dyeing is the consumption of energy and additives. Spinning before dyeing reduces the dyeing process of dyeing and finishing equipment and multi-channel fibers or fabrics, removes the dyeing auxiliaries, combines each pigment molecule into the target product, fundamentally eliminates the dye discharge, reduces the consumption of raw materials, To avoid environmental pollution, reducing the cost of dyeing, saving a huge amount of pollution control costs, there are reports, "polyester spinning before coloring and fiber dyeing compared to the production of 100 tons of liquid dyeing polyester staple fiber can save 10,000 tons of water, saving Gas 16,500 cubic meters, saving electricity 5.6 million degrees. "" Fiber dyeing per 100 kilograms of products, can produce about 10 tons of wastewater. " According to the survey, dyeing average t coloring fee of 4,000 yuan or so, and the use of masterbatch spinning before coloring, the tanning cost of the average cost of only 1,200 yuan, we can see spinning before the coloring not only saves a lot of pollution charges, and coloring costs only Of the third, that is, the cost of dyeing to more than three times the color of the liquid.
(3) high coloring quality
Conventional dyeing is mainly carried out using high temperature and high pressure conditions as described above using disperse dyes. However, due to the production of fiber and physical and chemical treatment is difficult to ensure that the internal structure of the crystal area and the uniform distribution of the area, the dye crystal, dispersion, dyeing rate and other general are often different, so the dyeing process is often easy to produce Color, stain, color flowers and other dyeing defects. Spinning before spinning is the coloring agent and the true color of the slices before the spinning, evenly mixed, and then by the melt filter, and then spinning, so the fiber dyeing uniform, regardless of batch size, color uniformity can be maintained, batch and The batch will not appear between the unacceptable color. From the structure of the fiber before dyeing, the colorant and the polyester form a consistent uniform solid solution, light fastness, washability, friction resistance and other fastness than conventional dyeing.
(4) environmental protection is good, good for health
The coloring agent used before dyeing is solvent dye, does not contain the structure and composition of the disabled, the human body does not cause harm. At the same time as the dyeing before dyeing can withstand more than 300 ℃ high temperature, spinning process without any gas and wastewater discharge, dye utilization increased to 100%, therefore, masterbatch color can be said to be environmentally friendly, health products.
(1) easy to use
Spinning before the color of polyester production, fiber use without any special requirements, the original spinning equipment, the existing production process. Especially when the polyester and other fibers blended intertwined, the use of polyester fiber does not only reduce the dyeing process, so that is not suitable for high temperature, high pressure dyeing conditions of fiber and polyester blended intertwined and easy to achieve the fabric pre-designed style. So before the spinning color to a certain extent, it can be said that no investment in the dyeing plant, is to use advanced technology to solve the dyeing and finishing "bottleneck" one of the shortcuts.
(2) low cost:
The cost of dyeing is the consumption of energy and additives. Spinning before dyeing reduces the dyeing process of dyeing and finishing equipment and multi-channel fibers or fabrics, removes the dyeing auxiliaries, combines each pigment molecule into the target product, fundamentally eliminates the dye discharge, reduces the consumption of raw materials, To avoid environmental pollution, reducing the cost of dyeing, saving a huge amount of pollution control costs, there are reports, "polyester spinning before coloring and fiber dyeing compared to the production of 100 tons of liquid dyeing polyester staple fiber can save 10,000 tons of water, saving Gas 16,500 cubic meters, saving electricity 5.6 million degrees. "" Fiber dyeing per 100 kilograms of products, can produce about 10 tons of wastewater. " According to the survey, dyeing average t coloring fee of 4,000 yuan or so, and the use of masterbatch spinning before coloring, the tanning cost of the average cost of only 1,200 yuan, we can see spinning before the coloring not only saves a lot of pollution charges, and coloring costs only Of the third, that is, the cost of dyeing to more than three times the color of the liquid.
(3) high coloring quality
Conventional dyeing is mainly carried out using high temperature and high pressure conditions as described above using disperse dyes. However, due to the production of fiber and physical and chemical treatment is difficult to ensure that the internal structure of the crystal area and the uniform distribution of the area, the dye crystal, dispersion, dyeing rate and other general are often different, so the dyeing process is often easy to produce Color, stain, color flowers and other dyeing defects. Spinning before spinning is the coloring agent and the true color of the slices before the spinning, evenly mixed, and then by the melt filter, and then spinning, so the fiber dyeing uniform, regardless of batch size, color uniformity can be maintained, batch and The batch will not appear between the unacceptable color. From the structure of the fiber before dyeing, the colorant and the polyester form a consistent uniform solid solution, light fastness, washability, friction resistance and other fastness than conventional dyeing.
(4) environmental protection is good, good for health
The coloring agent used before dyeing is solvent dye, does not contain the structure and composition of the disabled, the human body does not cause harm. At the same time as the dyeing before dyeing can withstand more than 300 ℃ high temperature, spinning process without any gas and wastewater discharge, dye utilization increased to 100%, therefore, masterbatch color can be said to be environmentally friendly, health products.
Lastest News
- Safe travel escort | Jincai New materials to carry out a full range of vehicle maintenance
- The characteristics of polypropylene masterbatch are mainly reflected in the following asp
- The operation of the textile industry from January to October 2024!
- National fire · life first | Golden Color New Materials Union participated in the 10th Yua
- What are the advantages of polypropylene masterbatches?
- Textile industry leads new quality productivity!
- Transformation and upgrading of textile and garment industry!
- Golden Color New Materials congratulates 2024 National plastic coloring and color masterba
- Plastic exhibition ended successfully | Golden Color won the honorary title of
- The operation of the textile industry from January to August 2024!