- Safe travel escort | Jincai New materials to carry out a full range of vehicle maintenance knowledge and skills training!
- The characteristics of polypropylene masterbatch are mainly reflected in the following aspects.
- The operation of the textile industry from January to October 2024!
- National fire · life first | Golden Color New Materials Union participated in the 10th Yuan Hua Town staff fire emergency skills Competition!
- What are the advantages of polypropylene masterbatches?
- Textile industry leads new quality productivity!
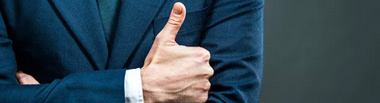
- Contact: Ms. Yang
- Phone: 0086-159 8831 5556
- Tel: 0086-573-87656555
- Fax: 0086-573-87659333
Different functions of masterbatch, the choice of paint, the performance is different, the following were introduced under the functional masterbatch how to choose the pigment:
Heat-resistant masterbatch The choice of pigments, the most basic requirements of the polypropylene fiber production process can withstand the temperature, to maintain its stability. Temperature temperature is generally required for the 270 ~ 280 ℃ above.
Masterbatch coloring is now the most commonly used plastic coloring method. The coloring agent dispersed in the carrier, and the masterbatch color resin simple mixed for the manufacture of plastic products. The pigment is mixed with the colorant and the colorant to be granulated into colored plastic, and is used in the molding process. Dry powder coloring: the powdery colorant and color resin evenly mixed directly after the manufacture of plastic products.
Dispersible color masterbatch pigment should be excellent in dispersibility, and in the masterbatch to be dispersed evenly, and the use of dispersants will not reduce the quality of polypropylene fiber or else can not produce good quality liquid stained liquid, the operation is not stable , It is easy to break or produce abnormal fibers when drawing fibers.
Brightness Polypropylene liquid coloring has a variety of uses, which are used for bedspreads and knitted fabrics, require bright colors. Because organic pigments are bright and bright, and easy to color, so that the use of organic pigments for the use of the above.
Light resistance In the light of the role of some pigments have photosensitive effect, so that coloring fiber fade and fragile, and the light resistance of the pigment is basically related to its chemical structure, so in the production of masterbatch should pay full attention to the light resistance, Of the pigment need to be used, you can consider adding UV absorbers.
- Safe travel escort | Jincai New materials to carry out a full range of vehicle maintenance
- The characteristics of polypropylene masterbatch are mainly reflected in the following asp
- The operation of the textile industry from January to October 2024!
- National fire · life first | Golden Color New Materials Union participated in the 10th Yua
- What are the advantages of polypropylene masterbatches?
- Textile industry leads new quality productivity!
- Transformation and upgrading of textile and garment industry!
- Golden Color New Materials congratulates 2024 National plastic coloring and color masterba
- Plastic exhibition ended successfully | Golden Color won the honorary title of
- The operation of the textile industry from January to August 2024!