- Safe travel escort | Jincai New materials to carry out a full range of vehicle maintenance knowledge and skills training!
- The characteristics of polypropylene masterbatch are mainly reflected in the following aspects.
- The operation of the textile industry from January to October 2024!
- National fire · life first | Golden Color New Materials Union participated in the 10th Yuan Hua Town staff fire emergency skills Competition!
- What are the advantages of polypropylene masterbatches?
- Textile industry leads new quality productivity!
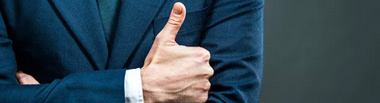
- Contact: Ms. Yang
- Phone: 0086-159 8831 5556
- Tel: 0086-573-87656555
- Fax: 0086-573-87659333
As technology advances,
People demand for daily necessities and clothing gradually high up,
More and more people begin to pay attention to the additional function of the product,
For example, whether anti-static, anti-UV, antibacterial, etc.,
So led to the development of functional masterbatch.
Functional masterbatch refers to a variety of plastic additives or chemical fiber concentrates, the color is generally white or translucent, direct additives in the form of masterbatch is not easy to disperse.
Common Masterbatch antibacterial masterbatch, flame retardant masterbatch, antistatic masterbatch, filled masterbatch, masterbatch cooling, anti-formaldehyde masterbatch, UV masterbatch, far infrared masterbatch, hydrophilic masterbatch, soft mother Tablets, negative oxygen ion masterbatch and so on. Today, a brief introduction to the color gold common masterbatch ~
Various antibacterial agents are uniformly dispersed in the matrix resin to make a concentrated body, that is, antibacterial masterbatch. After a certain amount of antibacterial masterbatch and the corresponding resin particles are blended, plastic parts, articles and antibacterial fibers with the antibacterial effect (bactericidal and bacteriostatic) on the surface can be prepared according to the processing and shaping methods of plastic and fiber.
Flame retardant masterbatch added products in the face of fire, the flame can automatically block the spread of the products will be burned after burning will not burn, played a role in flame retardant.
Under normal circumstances, flame-retardant masterbatch after special treatment, can improve its compatibility with the plastic resin, making it in the resin even if the amount added is not prone to delamination, blooming, patterns and other issues.
Through the addition of flame-retardant masterbatch to the general plastic with or close to the application requirements of engineering plastics, increased product added value, reducing raw material costs.
Filling masterbatch is a kind of white micron calcium carbonate masterbatch with pure raw material PE, PP or styrene resin as its carrier. The mesh number of calcium carbonate is determined by the user, and has good properties, dispersibility and stability without affecting the processing Machine screw precision.
Such masterbatch can be widely used in various plastic products such as PE, PP, PS, ABS and the like, such as PE plastic bags, injection molding, extrusion and other products, in particular, environmentally friendly plastic products that can be incinerated to achieve cost reduction purpose.
Anti-static masterbatch carrier and antistatic system is high-speed mixing, extrusion molding, and then diced to reduce the surface resistance of the material. Anti-static masterbatch is mainly used in chemical fiber clothing, plastic products and other fields, can make the surface resistance of 108-10Ω, with good anti-static effect.
The product added to the plastic or chemical fiber material to avoid the static electricity due to the polymer itself insulation so that it can adapt to product packaging requirements and special anti-static products, the product has good effect on the surface dust.
Antibacterial anti-formaldehyde masterbatch can effectively degrade formaldehyde, benzene, toluene, xylene, ammonia TVOC and other pollutants, and has a wide range of efficient disinfection; Toilet trash, animal odor produced with reduced efficacy.
Anti-formaldehyde masterbatch in the reaction process, the masterbatch itself will not change and loss, under the action of light can continue to purify the air. Has the advantage of lasting time and lasting effect. Anti-formaldehyde masterbatch non-toxic, harmless, safe and reliable to the human body. The final reactant is carbon dioxide and water, will not produce secondary pollution.
Cooling masterbatch is used in the early PP spinning process, in order to reduce the high viscosity of PP, to prevent other additives at high processing temperatures, such as pigment decomposition and dedicated. Cooling masterbatch can reduce the molecular weight of PP, thereby reducing the PP processing temperature.
Its main ingredient is peroxide. At present, the application range of the cooling masterbatch has been expanded, and has become a commonly used auxiliary for some PP modified production enterprises, and is most commonly used in the production of high-flow PP such as thin-wall storage drums in supermarkets.
Mainly used for cooling masterbatch used in polypropylene spinning. Due to the higher molecular weight polypropylene, spinning temperature up to 300 ℃ or more. This easy to make additives, pigments and other decomposition. Cooling masterbatch can generally reduce the spinning temperature of 10 ~ 50 ℃, improve the spinning process.
Zhejiang Jin Cai New Materials Co., Ltd. specializes in producing a variety of masterbatch, masterbatch produced by the effect of good, lasting long-lasting, decentralized, add small and does not contain any toxic substances, can be applied to a wide range.
Jin Cai functional masterbatch through supporting spinning proofing machine, injection molding machine, DF value detector and a series of development testing equipment, sample production, marketing and service are in accordance with the ISO9001: 2008 quality management system implementation. Has a strong sales force, improve management and after-sales service.
- Safe travel escort | Jincai New materials to carry out a full range of vehicle maintenance
- The characteristics of polypropylene masterbatch are mainly reflected in the following asp
- The operation of the textile industry from January to October 2024!
- National fire · life first | Golden Color New Materials Union participated in the 10th Yua
- What are the advantages of polypropylene masterbatches?
- Textile industry leads new quality productivity!
- Transformation and upgrading of textile and garment industry!
- Golden Color New Materials congratulates 2024 National plastic coloring and color masterba
- Plastic exhibition ended successfully | Golden Color won the honorary title of
- The operation of the textile industry from January to August 2024!